Ein Bericht von Yannik Weber, Uhrmacher Auszubildender, 15. April 2023
Am Anfang steht die Planung
Die Zähnezahl und der Modul sollten mindestens bekannt sein. Ferner noch die
Abmessungen des Triebes, auf welches das Rad aufgenietet werden soll. Dann beginnt
das Ausrechnen der fehlenden Größen:
- Teilkreisdurchmesser = Modul•Zähnezahl
- Kopfkreisdurchmesser = (Zähnezahl +2,76)•Modul
- Fußkreisdurchmesser = (Zähnezahl-3,14)•Modul
- Zahnhöhe = (Kopfkreisdurchmesser-Fußkreisdurchmesser):2
- Breite des Zahngrundes = Zahnhöhe •1,627
- Innenradius = Fußkreisdurchmesser-2•Breite des Zahngrundes
- Kernradius = Teilkreisradius des Triebes•1,5
- Schenkelbreite = (3:7)•(Innenradius-Kernradius)
Nachdem alle Werte ausgerechnet wurden wird noch eine Zeichnung in
geeignetem Vergrößerungsmaßstab erstellt.
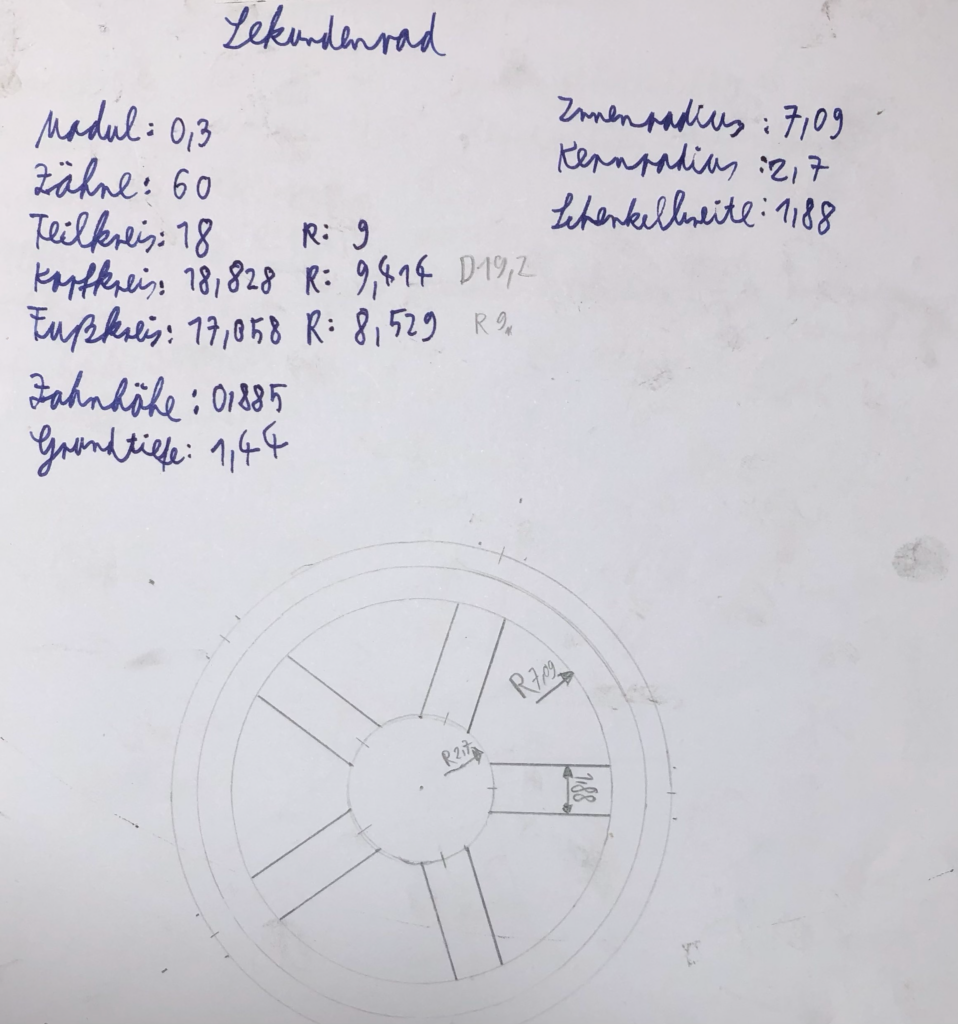
Die Anfertigung
Dann kann mit der Arbeit begonnen werden. Zunächst wird ein Stück Messingblech grob zugeschnitten und beidseitig abgeschliffen, um Spannungen aus dem Material zu nehmen und plane Oberflächen zu erhalten.
Anschließend wird das Rad mit Zirkel, Reißnadel und Stahllineal angerissen. Dazu wird das Blech zunächst mit einem Filzstift schwarz angemalt um die Anreißlinien besser erkennen zu können. Um den Zirkel sauber ansetzen zu können, sollte vorher noch
gekörnt werden.
Möchte man den Zirkel möglichst genau einstellen, so kann man sich behelfen, indem man das gewünschte Maß zunächst mit dem Höhenreiser auf
einem Stück Blech anreist und dann mit dem Zirkel abgreift.
Nachdem alle Kreise gezeichnet wurden, gilt es die Schenkel anzureisen. Hierzu müssen weitere Berechnungen vorgenommen werden.
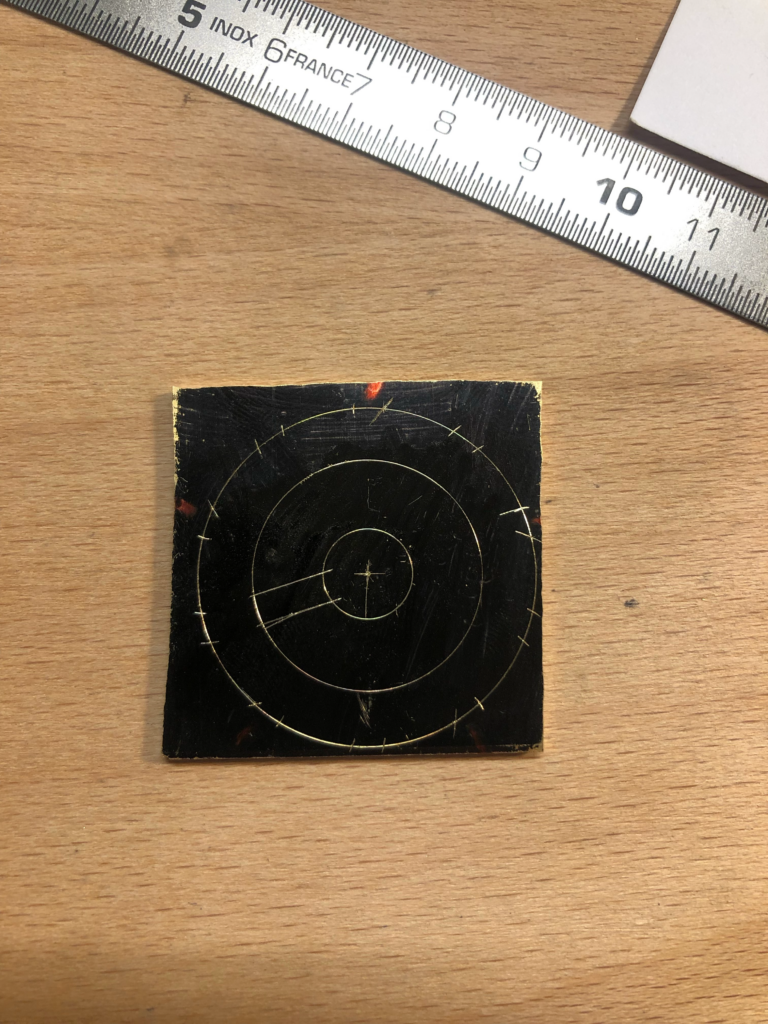
Das Rad soll fünf Schenkel erhalten. Um diese durch die Mitte anreisen zu können muss der Kreis in zehn gleiche Teile geteilt werden, also jeweils 36 Grad. Mit Hilfe des Cosinussatzes wird der Abstand zweier benachbarter Punkte auf dem Kreisumfang ausgerechnet. Die Formel lautet: X=r^2•r^2–2•r•r•cos(36)
Das gefundene Maß wird am Zirkel eingestellt und an einer beliebigen Stelle des Kreises angesetzt. Jetzt arbeitet man sich von einem Punk zum nächsten bis der Kreis geschlossen ist. Sollte man hierbei nicht wieder genau auf den Anfangspunkt stoßen, kann man die Einstellung des Zirkels leicht korrigieren und etwas versetzt einen neuen Versuch starten. Die alten Markierungen sind dabei zu übermalen.
Nach diesem Arbeitsschritt wird der Zirkel auf die Schenkelbreite eingestellt und von jedem Punkt aus ein weiterer Anriss vorgenommen. Jetzt können die Punkte mit dem Stahllineal und der Reisnadel verbunden werden.
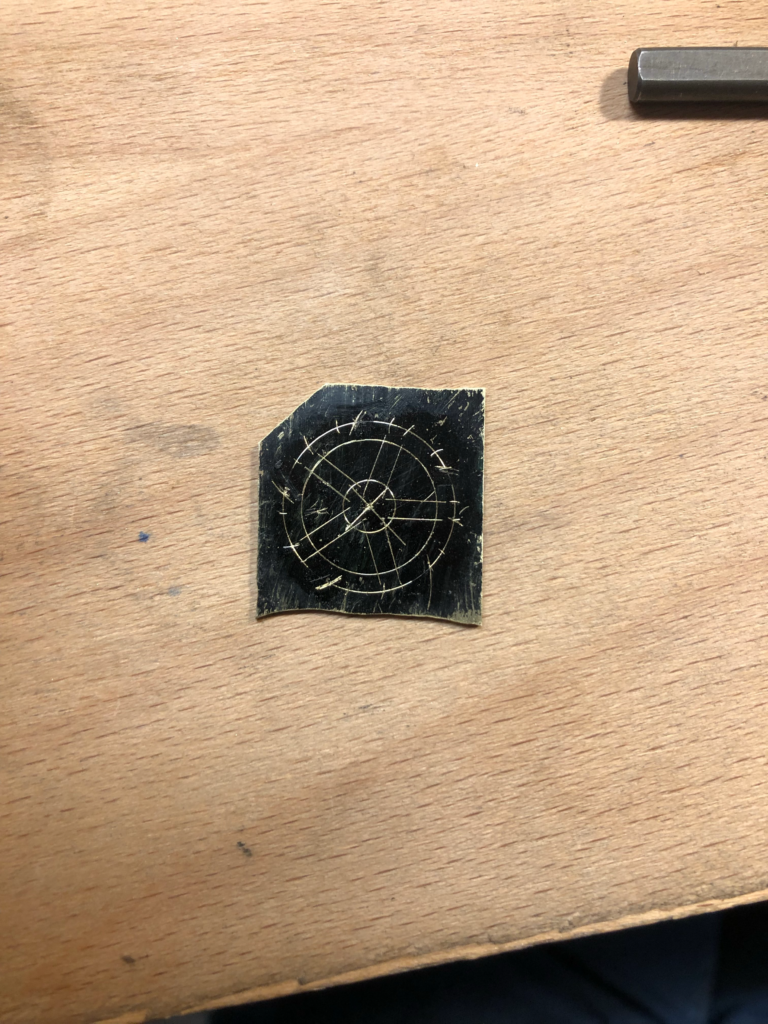
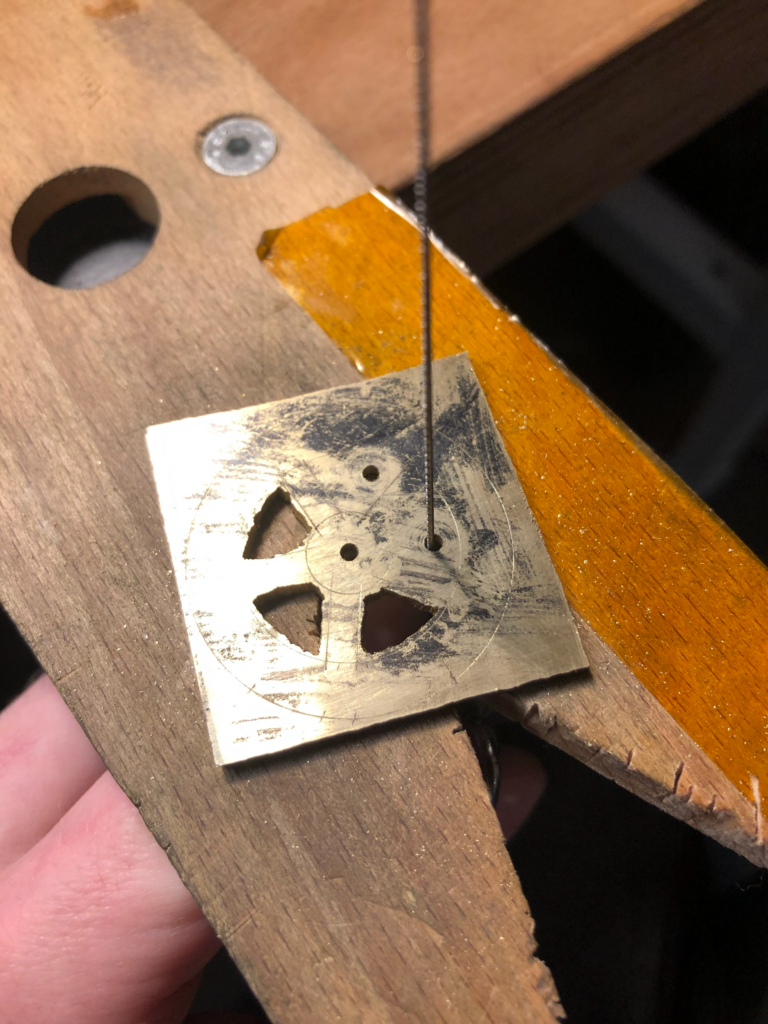
Als nächstes werden Löcher gebohrt: zunächst ein kleines in der Mitte und eines in jeden Zwischenraum zwischen den Schenkeln. Anschließend wird begonnen die Form grob auszusägen. Besonders außen sollte ein reichliches Übermaß zum Runddrehen und später zum Verzahnen stehen bleiben.
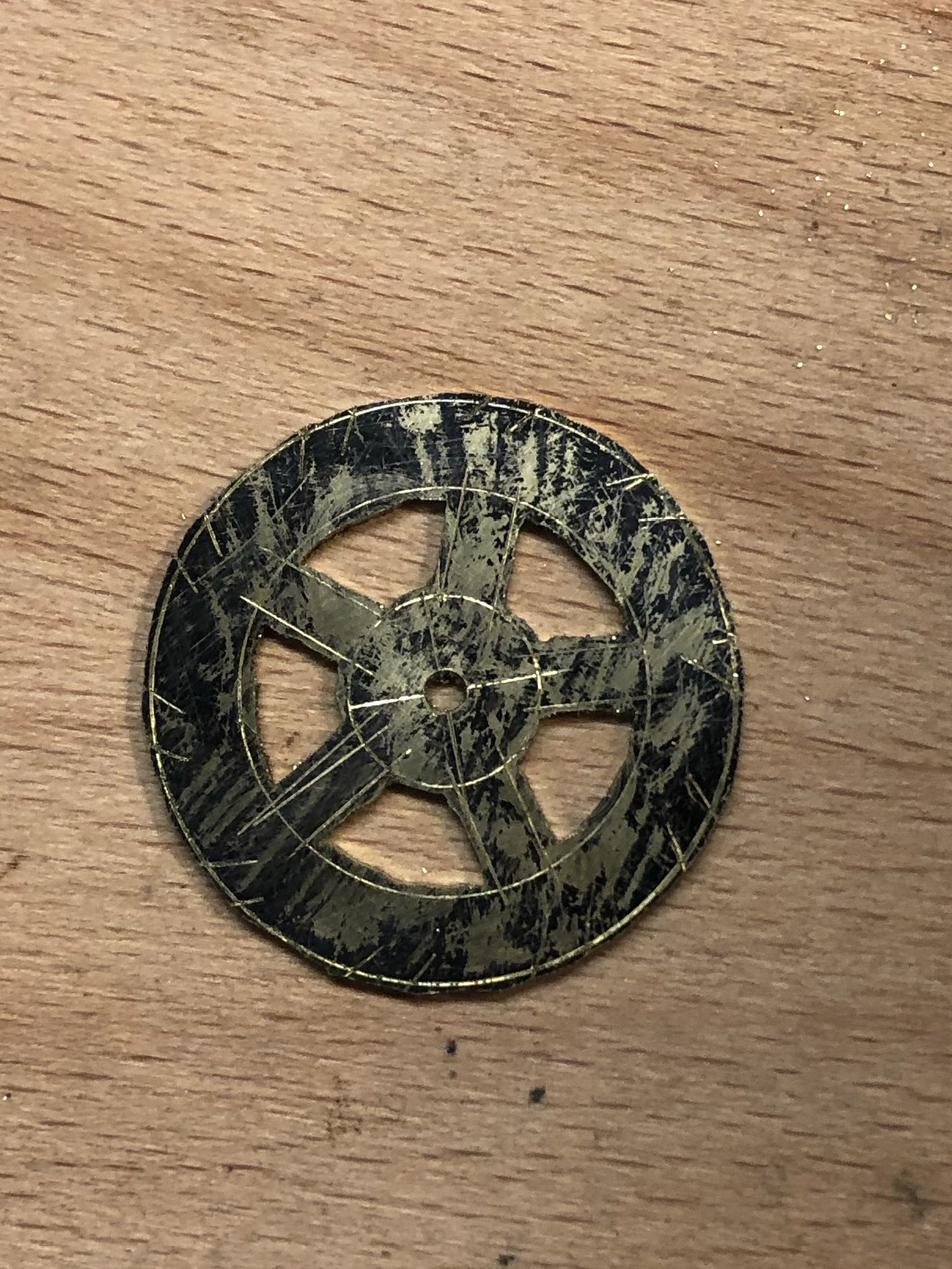
Anschließend wird das Rad rund gedreht. Dazu wird es auf einen Drehstift oder eine Lackscheibe aufgespannt. Das angestrebte Maß sollte gut einen halben Millimeter größer sein als der spätere Kopfkreisdurchmesser. Die Schenkel des Rades werden nun noch mit immer feiner werdenden Feilen in ihre endgültige Form gebracht. Dabei kann mit einem Messschieber nachgemessen werden, wichtiger ist aber dass das Rad gleichmäßig aussieht.
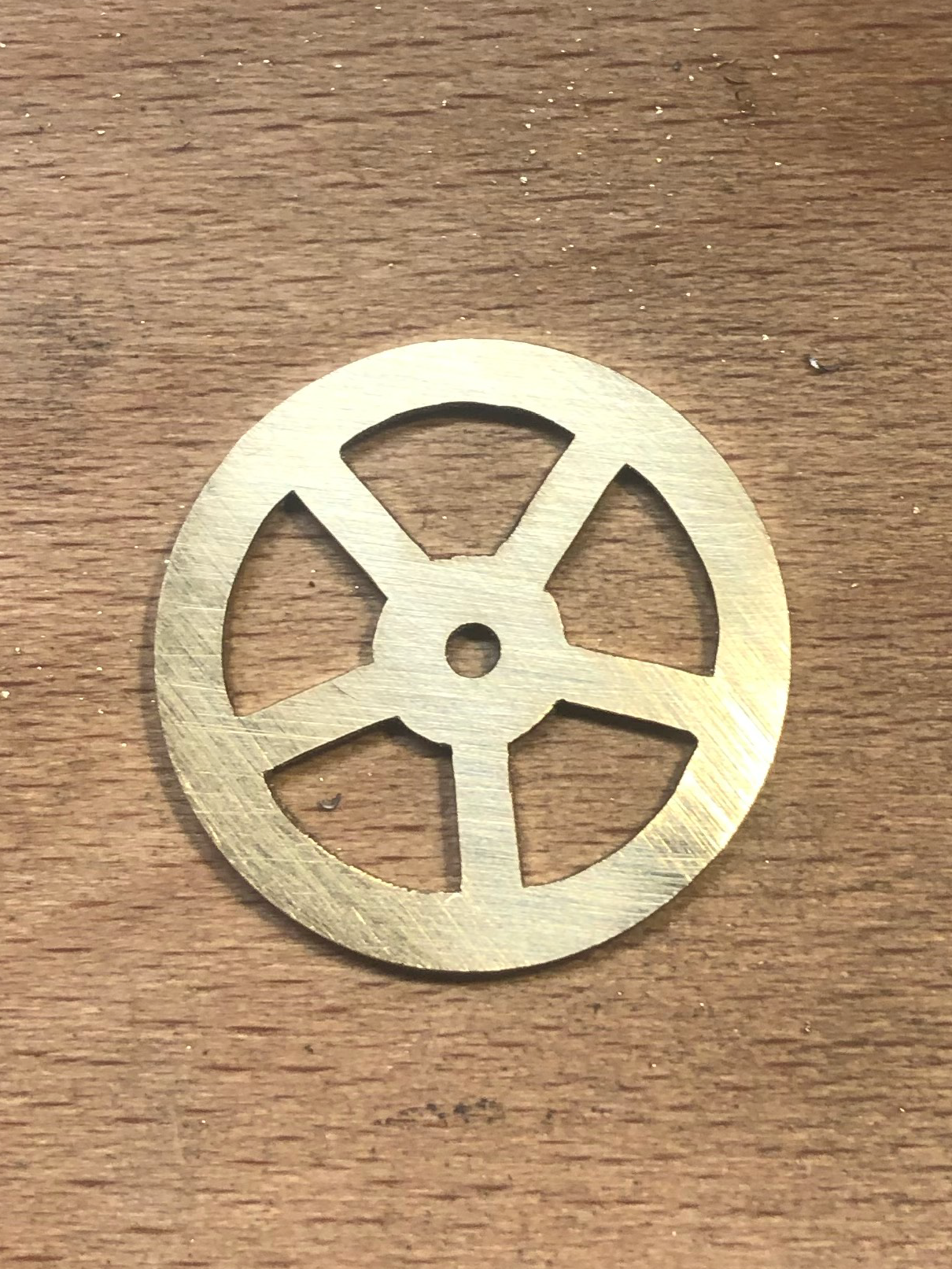
Nach diesem Arbeitsschritt wird das Rad nochmals beidseitig abgeschliffen um Reste von Anreisslinien zu entfernen und schließlich werden alle Kanten entgratet.
Es empfiehlt sich noch einige Messingscheiben mit gleichem Außendurchmesser anzufertigen, um beim Verzahnen ein paar Probestücke zu haben.
Jetzt wird das Rad in das Sechsbackenfutter der Drehbank gespannt und das mittlere Loch auf den Teilkreisdurchmesser des Triebes aufgebohrt, sofern das Rad auf einen Trieb aufgenietet werden soll. Hierbei sollte möglichst kleinschrittig vorgegangen werden, um ein Herausreißen des Rades aus dem Futter zu vermeiden.
Danach muss das Loch beidseitig entgratet werden.
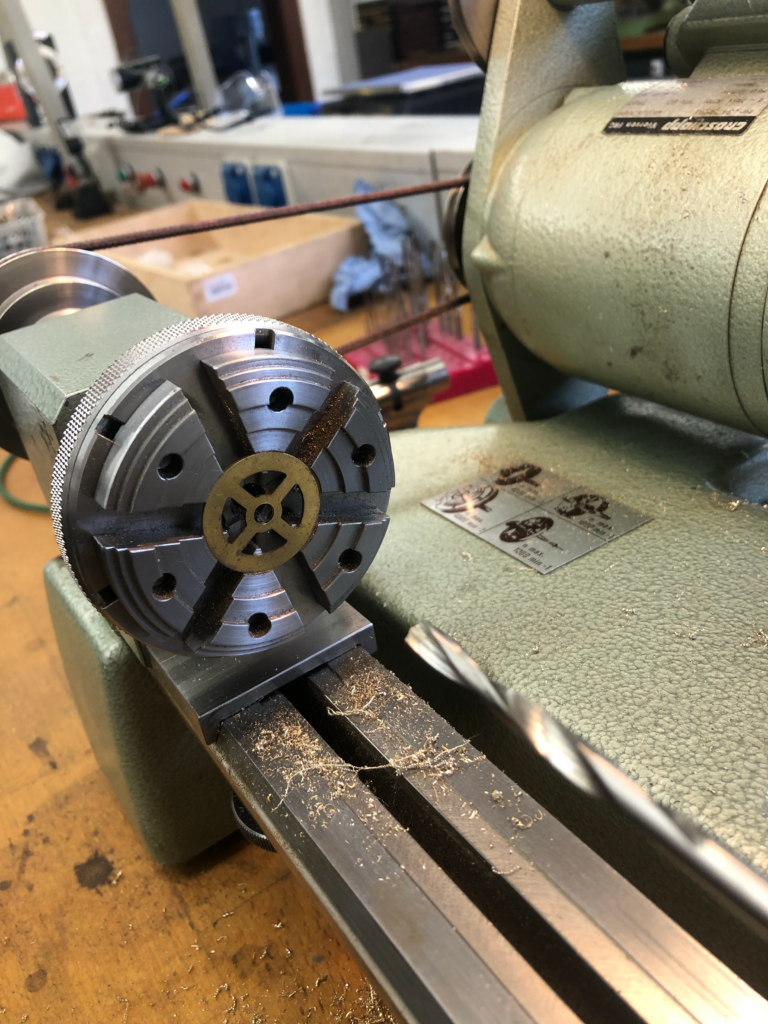
Um das Rad verzahnen zu können muss eine Aufnahme gedreht werden. Diese benötigt an einer Seite einen Ansatz, der in eine Spannzange passt und an der anderen Seite
einen Ansatz, auf den sich das Rad spielfrei aufschieben lässt. Der mittlere Teil sollte
etwas dünner als der Fußkreisdurchmesser sein. Als Gegenstück zu diesem Aufnahmedorn ist eine Art Glocke zu drehen, die außen so dick ist wie der dickste
Durchmesser des Aufnahmedorns, des Weiteren benötigt sie eine Ausdrehung und
ein mittiges Loch, welches etwas größer als das Loch im Rad sein sollte.
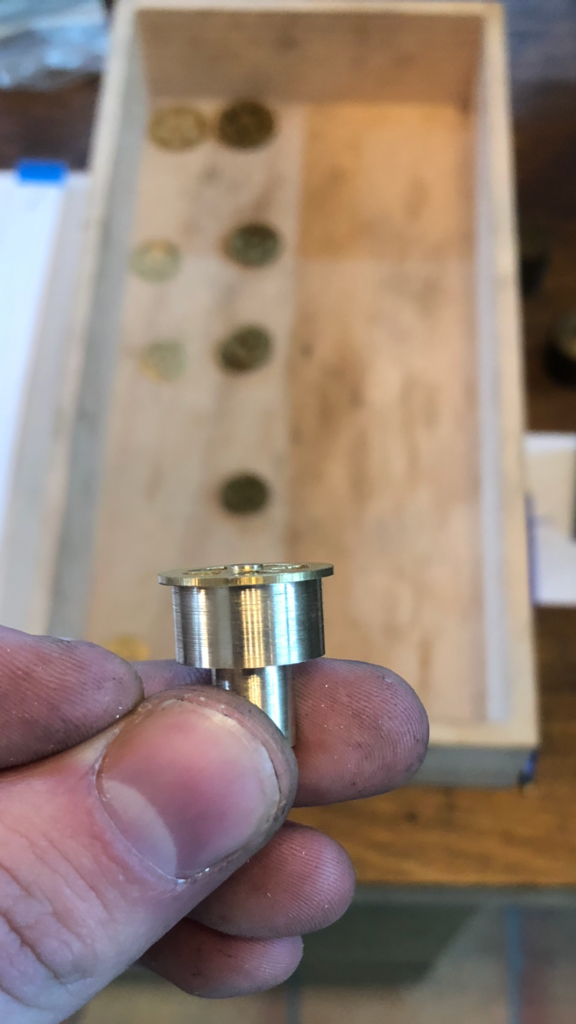
Nun gilt es die Maschine einzurichten. Zunächst wird in der Tabelle nachgeschlagen, welche Wechselräder für die gewünschte Zahnzahl verwendet werden müssen. Als nächstes muss ein passender Fräser ausgewählt werden, der dem gewünschten Modul entspricht und den Bereich der Zahnzahl abdeckt. Eventuell muss jetzt noch eine Hülse gedreht werden, um den Fräser in die Maschine spannen zu können. Nachdem Fräser und Wechselräder montiert wurden, wird durch die dafür vorgesehene Bohrung mit Hilfe einer feststehenden Spitze überprüft, ob der Fräser mittig steht. Ein weißes Blatt Papier erhöht dabei den Kontrast. Jetzt wird der Aufnahmedorn in die untere Spannzange eingespannt. Das Rad wird aufgelegt und mit Hilfe der Aufnahmeglocke und einer mitlaufenden Spitze gut fest geklemmt.
Das Fräsen kann beginnen. Der Fräser arbeitet dabei im Gegenlauf und sollte mit einer Fräspaste geschmiert werden. Er wird zunächst soweit zugestellt, bis die Zahnspitzen sauber geformt werden. Dann
wird das komplette Rad gefräst und der Durchmesser gemessen. Jetzt lässt sich
ermitteln, wie weit noch zugestellt werden muss, um den gewünschten
Kopfkreisdurchmesser zu erhalten.
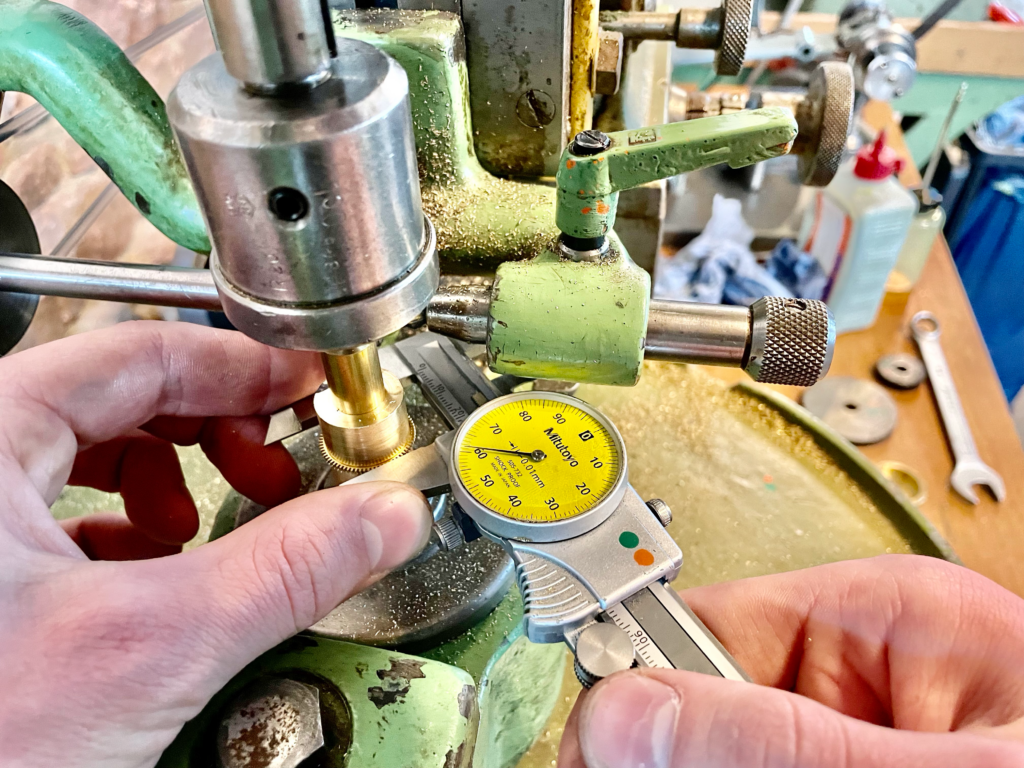
Nachdem nun alle Zähne nochmal nachgefräst wurden, sollte der gewünschte Durchmesser erreicht sein. Das Rad kann ausgespannt und auf einer Schleifplatte entgratet werden. Unterm Mikroskop zeigt sich nun, ob die Verzahnung in Ordnung ist, oder ob noch feine Korrekturen an der Maschine vorgenommen werden müssen.
Wenn alles passt können die restlichen Rohlinge in jeweils einem Durchgang verzahnt
werden. Dabei können auch mehrere Rohlinge übereinander eingespannt werden.
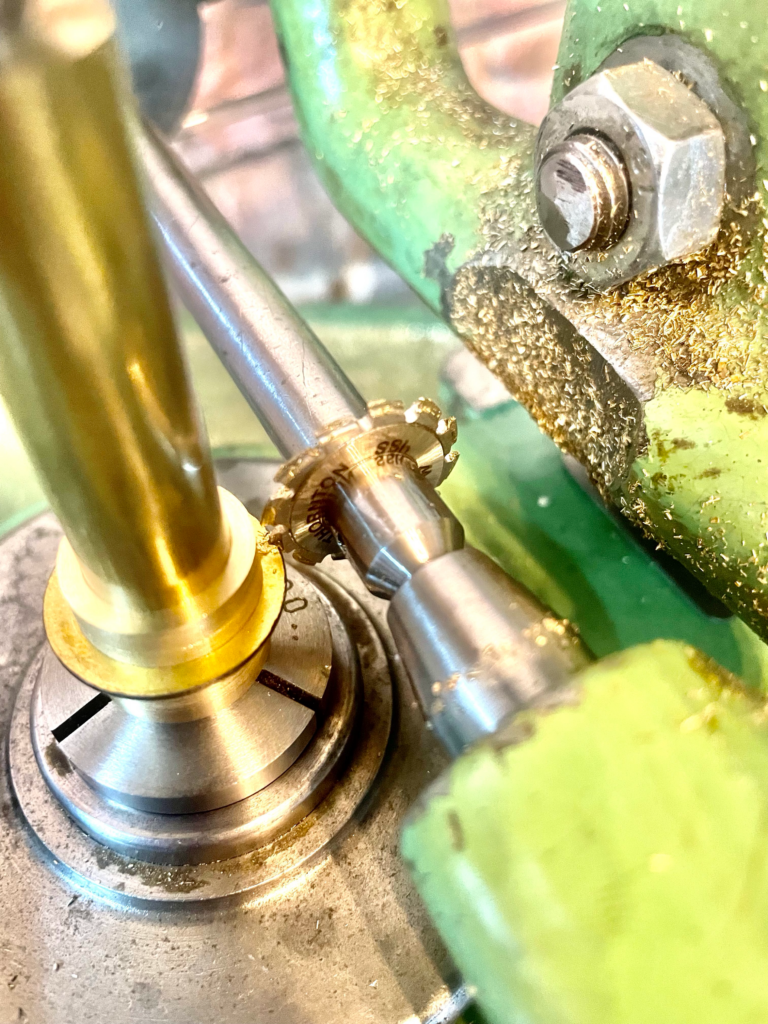
Nachdem das Fräsen abgeschlossen ist werden alle Räder plan geschliffen und
anschließend mit einem Zierschliff versehen.
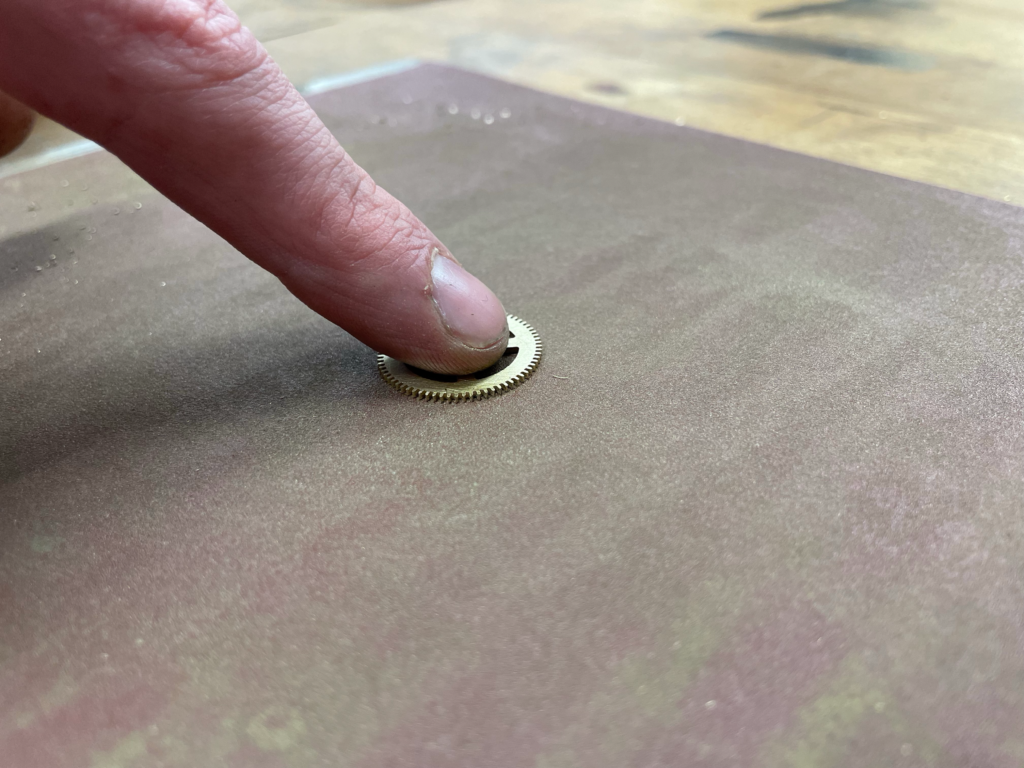
Dazu werden sie entweder mit einer
Schutzfolie ins Sechsbackenfutter gespannt oder mit doppelseitigem Klebeband auf
eine Lackscheibe geklebt. Dabei muss das Rad mit dem Bohrreitstock zentriert werden.
Jetzt wird die Drehbank angeschaltet und mit Schleifpapier ein Kreisschliff
aufgebracht. Danach werden die Räder im Ultraschallbad gereinigt. Mit einem
angeschliffenen Ölgeber wird jeder Zahn einzeln entgratet.
Zum Schluss werden die Räder noch einmal gereinigt.
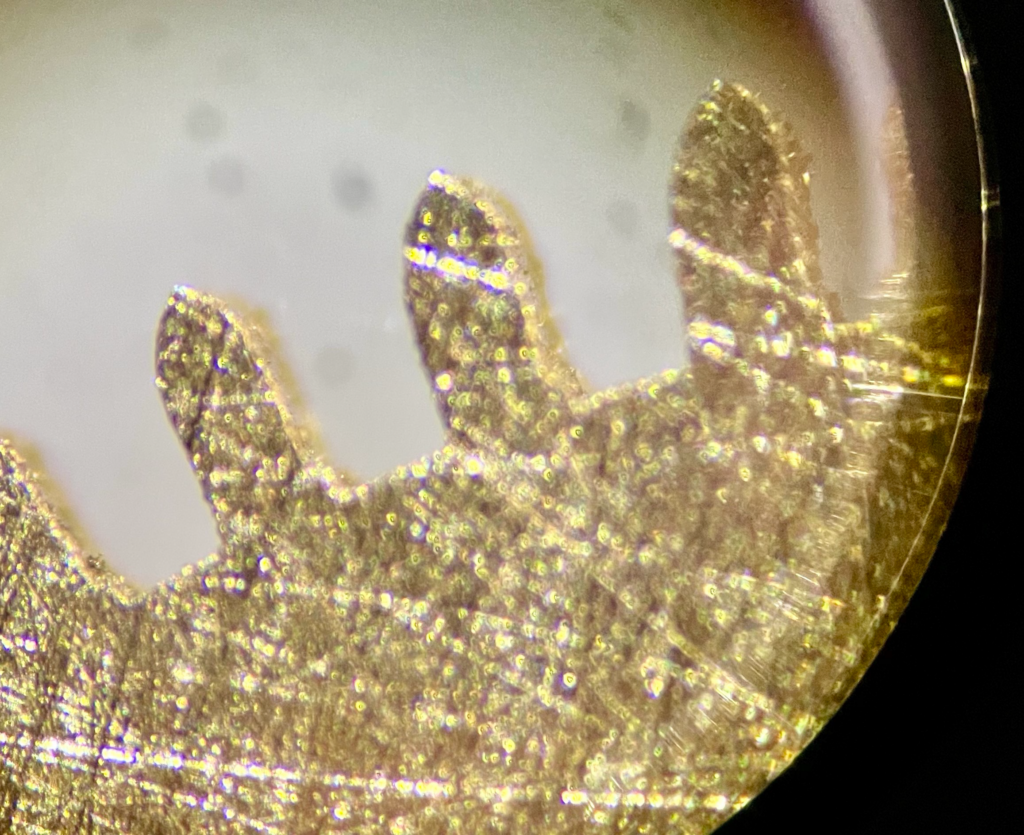
Schreibe einen Kommentar